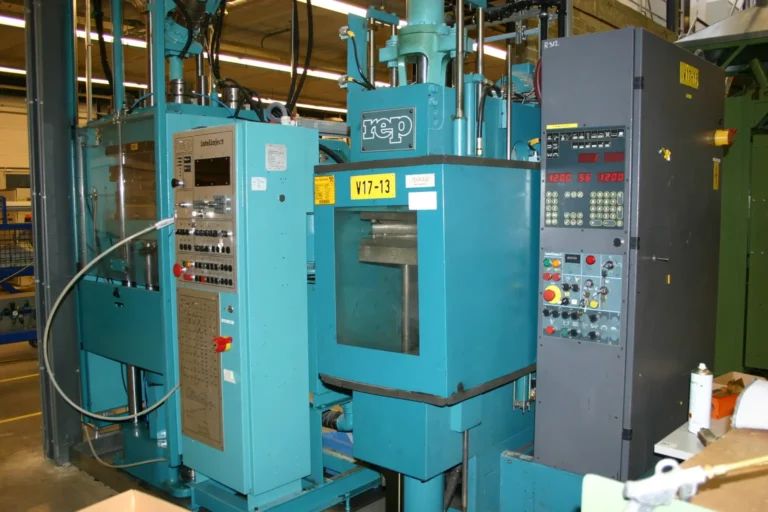
Enbi is an injection molding company that specializes in precision rubber products for a range of industries and demanding applications. Our injection molding services offer precision, efficiency, and scalability to meet your needs. Whether you require complex components or standard parts, Enbi delivers reliable, cost-effective solutions.
Our service is ideal for high-volume production runs and complex parts with tight tolerances, making it suitable for industries like medical, aerospace, renewable energy automotive and consumer products. With faster cycle times, high precision, and minimal waste, our injection molding solutions support efficient manufacturing.
Enbi is a trusted injection molding partner, focused on consistent, high-quality results. Contact us today to learn how our injection molding services can meet your business needs.
Injection molding is a manufacturing process used to create parts by injecting heated material into a mold. This process is commonly used for producing rubber, plastic, and other polymer components. It starts by heating the material until it becomes molten (liquid), making it suitable for easy flow and shaping. This molten material is then injected into a precisely designed mold cavity under high pressure, where it cools and solidifies into the desired shape.
Injection molding is versatile and ideal for producing both simple and complex parts. It supports high-volume production with consistent quality, making it suitable for industries such as automotive, consumer goods, medical devices, and electronics. This process is particularly beneficial for manufacturing intricate components that require tight tolerances.
One key advantage of injection molding is its efficiency in large production runs, ensuring minimal waste, high repeatability, and lower labor costs. Molds can be made to exact specifications, allowing manufacturers to produce identical parts with precision.
Overall, injection molding is a reliable method for creating durable, high-quality components and is a preferred choice for manufacturers needing scalability and accuracy.
BENEFITS OF INJECTION MOLDING
Injection molding offers key advantages, especially for high-quality rubber components. These benefits improve efficiency for manufacturers like Enbi and allow us to pass on cost savings to clients. Here are the main benefits of Enbi’s injection molding services:
High Efficiency and Fast Production
Enbi’s injection molding is highly automated, reducing manual labor and ensuring short production cycles. This efficiency enables quick, cost-effective production of large volumes.
Precision and Consistency
Our process allows precise control, achieving tight tolerances and producing intricate parts with consistent quality.
Reduced Waste
Enbi’s injection molding uses only the material needed, minimizing waste and reducing excess material, commonly known as flash.
Material Versatility
We work with various rubber materials, including natural rubber, silicone, EPDM, and nitrile, tailored to specific requirements like heat resistance or elasticity.
Enhanced Mechanical Properties
Our process ensures parts with uniform strength and durability, offering superior mechanical properties compared to other rubber manufacturing methods.
Lower Labor Costs
Automation reduces manual handling, resulting in lower labor costs and increased efficiency.
Scalability
Enbi’s injection molding is ideal for mass production, providing a scalable solution for high-volume manufacturing with consistent quality.
Reduced Cycle Time
Fast curing times reduce cycle times as rubber is injected into a heated mold, making the process faster than methods like compression or transfer molding.
Fewer Defects
Injection molding minimizes variability, leading to fewer defects, such as voids or incomplete mold filling, ensuring high-quality components.
Environmental Benefits
With minimal waste and recyclable scrap material, injection molding has a lower environmental impact than other manufacturing methods.
These benefits make Enbi’s injection molding services ideal for efficiently producing durable, high-quality rubber parts for industries like automotive, healthcare, electronics, and consumer goods.
THE INJECTION MOLDING PROCESS
Injection molding is an efficient manufacturing method used to create rubber, plastic, and polymer parts by injecting molten material into a mold. Here’s how the injection molding process works:
- Material Preparation: The raw material is heated until it becomes molten, turning into a liquid suitable for precise shaping.
- Injection into Mold: The molten material is injected under high pressure into a precisely designed mold. This pressure ensures the material fills every part of the mold, resulting in detailed, consistent parts.
- Cooling and Solidifying: The material cools and solidifies in the mold, which includes channels for efficient cooling. This allows the part to harden quickly and accurately.
- Part Ejection: Once solidified, the mold opens, and the part is ejected. The cycle repeats, enabling rapid production of identical components.
This injection molding process is versatile, enabling Enbi to produce both simple and complex parts with precision. With the capacity for high-volume production, minimal waste, and quick turnaround times, our injection molding services offer a reliable, cost-effective solution for industries ranging from automotive to electronics.
Industries That Benefit from Injection Molding
Injection molding is a versatile process that serves many industries. Here are key sectors that benefit from Enbi’s injection molding services:
- Automotive: Essential for manufacturing durable components like seals, gaskets, and interior parts that require precision and resilience.
- Healthcare: Used for high-quality medical devices and components, including rubber seals, tubing, and other precise parts critical for medical applications.
- Consumer Goods: Enables the production of items with intricate designs, consistent quality, and cost-efficiency, from household products to electronics.
- Electronics: Produces parts such as casings, seals, and connectors that require detailed craftsmanship and reliability.
- Industrial Equipment: Creates components for industrial machinery that need strength and consistency to withstand harsh conditions.
These industries, and more, benefit from injection molding’s ability to produce complex parts with tight tolerances, precision, and repeatability. Enbi’s expertise ensures we meet the specific demands of each sector, delivering reliable, high-quality components for a variety of applications.
Rubber molding shapes rubber into specific forms using heat and pressure. Each molding technique suits particular applications, part complexity, production volume, and material properties. Here are the main rubber molding processes:
Injection Molding
- Process: Heated rubber is injected under high pressure into a mold cavity, where it fills the mold and cures.
- Best For: High-volume production, complex parts requiring tight tolerances.
- Advantages: Faster cycles, high precision, minimal waste, ideal for intricate designs.
- Disadvantages: Higher tooling and equipment costs, less suited for very large parts.
Transfer Molding
- Process: Rubber is placed in a chamber above the mold cavity and forced into the cavity by a plunger, curing inside the mold.
- Best For: Medium to high production volumes, complex parts, parts requiring metal inserts.
- Advantages: Better flash control, suited for parts with metal inserts or intricate shapes.
- Disadvantages: More waste than injection molding, complex tooling.
Compression Molding
- Process: Pre-heated rubber is placed in a mold cavity, then shaped under heat and pressure. The material cures in the mold, forming the final part.
- Best For: Low to medium production volumes, simple to moderately complex parts, materials with longer cure times (e.g., silicone).
- Advantages: Lower tooling costs, can produce large and thick parts.
- Disadvantages: Longer cycle times, less precision for complex shapes.
Blow Molding
- Process: A hollow parison is expanded inside a mold using pressurized air, shaping the rubber as it cools.
- Best For: Hollow parts like rubber bottles or bladders.
- Advantages: Efficient for creating hollow items.
- Disadvantages: Limited to hollow shapes, may lack dimensional precision.
Rotational Molding
- Process: A measured amount of rubber is heated and rotated in a mold, using centrifugal force to coat the inside evenly and form a hollow part.
- Best For: Large hollow parts, such as containers or automotive components.
- Advantages: Uniform wall thickness, economical for large items.
- Disadvantages: Slower cycle times, limited to hollow designs.
Liquid Injection Molding (LIM)
- Process: Liquid silicone rubber (LSR) is injected into a mold, where it is heated and cured. This process typically uses two-part liquid silicones for fast curing.
- Best For: High-volume production of precise parts, including medical and food-grade applications.
- Advantages: High precision, quick cycle times, suitable for intricate parts.
- Disadvantages: Requires specialized equipment and materials.
Extrusion Molding
- Process: Rubber is forced through a die to create continuous shapes like tubes or profiles, then vulcanized (cured) to maintain shape.
- Best For: Continuous lengths of rubber products, such as hoses, gaskets, and seals.
- Advantages: Ideal for long, uniform shapes, supports continuous production.
- Disadvantages: Limited to simpler shapes, requires cutting or trimming after molding.
Vacuum Molding
- Process: Rubber is placed in a sealed mold, and a vacuum removes air to ensure the rubber fills the cavity. Heat then cures the material.
- Best For: Intricate parts where air entrapment is a concern.
- Advantages: Reduces defects like air bubbles, produces a better surface finish.
- Disadvantages: Slower process, requires specialized equipment.
Each rubber molding technique offers unique benefits based on part design, material properties, production volume, and cost. Selecting the right process ensures optimal results for specific applications.
Get a Quotation
Let us know how to get back to you.
View our brochures download page to learn more about Enbi.
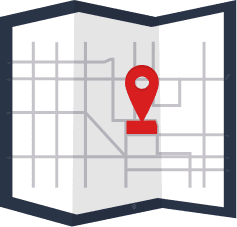
Find your local Enbi facility to enquire about our injection molding options.
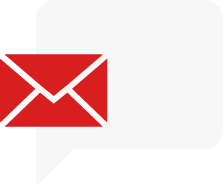
Urgent technical question? Contact our experienced engineers for advice.