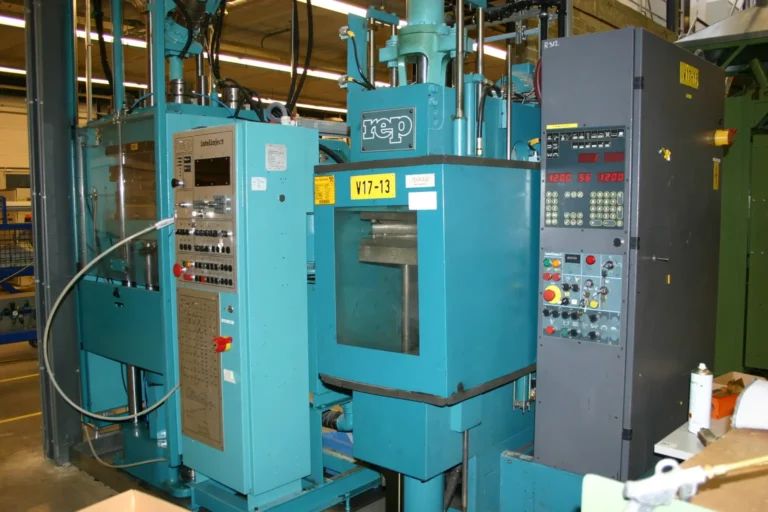
Enbi 是一家注塑公司,专门从事 精确 适用于各种行业的橡胶产品 和要求苛刻的应用. 我们的注塑服务提供精度、效率和可扩展性 满足您的需求.无论您需要复杂组件还是标准零件,Enbi 都能提供可靠、经济高效的解决方案。
我们的服务非常适合大批量生产和公差严格的复杂零件,适合以下行业: 医疗的, 航空航天、可再生能源 汽车和消费品。我们的注塑解决方案具有更快的循环时间、更高的精度和最少的浪费,支持高效制造。
Enbi 是值得信赖的注塑合作伙伴,专注于提供始终如一的高质量成果。立即联系我们,了解我们的注塑服务如何满足您的业务需求。
注塑成型是一种通过将加热的材料注入模具来制造零件的制造工艺。该工艺通常用于生产橡胶、塑料和其他聚合物部件。首先加热材料,直到其熔化(液体),使其易于流动和成型。然后将熔融材料在高压下注入精确设计的模具腔中,在那里冷却并凝固成所需的形状。
注塑成型用途广泛,是生产简单和复杂零件的理想选择。它支持大批量生产且质量始终如一,适合汽车、消费品、医疗设备和电子产品等行业。该工艺尤其适用于制造需要严格公差的复杂部件。
注塑成型的一个主要优势是其在大批量生产中的效率,可确保最少的浪费、高重复性和较低的劳动力成本。模具可以按照精确的规格制造,使制造商能够精确地生产相同的零件。
总体而言,注塑成型是制造耐用、高质量组件的可靠方法,也是需要可扩展性和准确性的制造商的首选。
注塑成型的优点
注塑成型具有关键优势,尤其是对于高品质橡胶部件而言。这些优势提高了 Enbi 等制造商的效率,并使我们能够将成本节省转嫁给客户。以下是 Enbi 注塑成型服务的主要优势:
高效快速生产
Enbi 的注塑成型高度自动化,减少了人工劳动,确保生产周期短。这种效率可实现快速、经济高效的大批量生产。
精确性和一致性
我们的工艺可以实现精确控制,达到严格的公差,并生产出质量稳定的复杂零件。
减少浪费
Enbi 的注塑成型仅使用所需的材料,最大限度地减少浪费并减少多余的材料(通常称为飞边)。
材料多功能性
我们使用各种橡胶材料,包括天然橡胶、硅胶、三元乙丙橡胶和丁腈橡胶,以满足耐热性或弹性等特定要求。
增强机械性能
我们的工艺确保零件具有均匀的强度和耐用性,与其他橡胶制造方法相比,具有优异的机械性能。
降低劳动力成本
自动化减少了人工操作,从而降低了劳动力成本并提高了效率。
可扩展性
Enbi 的注塑成型非常适合大规模生产,为质量一致的大批量生产提供了可扩展的解决方案。
缩短周期时间
由于橡胶被注入加热模具中,快速固化时间减少了循环时间,使得该过程比压缩或传递成型等方法更快。
更少缺陷
注塑成型最大限度地减少了变化性,从而减少了空隙或模具填充不完整等缺陷,确保了高质量的组件。
环境效益
由于废物最少且废料可回收,注塑成型对环境的影响比其他制造方法要小。
这些优势使 Enbi 的注塑服务成为高效生产汽车、医疗保健、电子和消费品等行业耐用、高品质橡胶零件的理想选择。
注塑成型工艺
注塑成型是一种高效的制造方法,通过将熔融材料注入模具来制造橡胶、塑料和聚合物部件。注塑成型工艺的工作原理如下:
- 材料准备:将原材料加热直至熔化,变成适合精确成型的液体。
- 注塑模具:熔融材料在高压下注入精确设计的模具中。这种压力确保材料填充模具的每个部分,从而产生精细、一致的部件。
- 冷却和凝固:材料在模具中冷却并凝固,模具内设有高效冷却通道。这样可使部件快速准确地硬化。
- 部件弹出:一旦凝固,模具就会打开,部件就会弹出。循环重复进行,从而能够快速生产相同的部件。
这种注塑成型工艺用途广泛,使 Enbi 能够精确生产简单和复杂的部件。凭借大批量生产能力、最少浪费和快速周转时间,我们的注塑成型服务为从汽车到电子等行业提供可靠、经济高效的解决方案。
受益于注塑成型的行业
注塑成型是一种多功能工艺,适用于许多行业。以下是受益于 Enbi 注塑成型服务的关键行业:
- 汽车:对于制造需要精度和弹性的密封件、垫圈和内部零件等耐用部件至关重要。
- 卫生保健:用于高质量医疗设备和组件,包括橡胶密封件、管道和其他对医疗应用至关重要的精密部件。
- 消费品:能够生产设计复杂、质量稳定且具有成本效益的物品,从家用产品到电子产品。
- 电子产品:生产需要精细工艺和可靠性的外壳、密封件和连接器等零件。
- 工业设备:为工业机械制造需要强度和一致性来承受恶劣条件的零部件。
这些行业以及其他行业都受益于注塑成型能够生产具有严格公差、精度和可重复性的复杂部件的能力。Enbi 的专业知识确保我们能够满足每个行业的特定需求,为各种应用提供可靠、高质量的组件。
橡胶成型利用热量和压力将橡胶塑造成特定形状。每种成型技术都适用于特定的应用、零件复杂性、生产量和材料特性。以下是主要的橡胶成型工艺:
注塑成型
- 过程: 加热的橡胶在高压下被注入模腔,然后填充模具并固化。
- 最适合: 大批量生产,复杂零件需要严格的公差。
- 优点: 周期更快、精度更高、浪费更少,适合复杂的设计。
- 缺点: 工具和设备成本较高,不太适合非常大的部件。
传递模塑
- 过程: 将橡胶放置在模具腔上方的腔室中,并通过柱塞将其压入腔内,在模具内部固化。
- 最适合: 中到高产量、复杂零件、需要金属嵌件的零件。
- 优点: 更好的闪光控制,适合带有金属嵌件或复杂形状的部件。
- 缺点: 比注塑成型浪费更多,工具复杂。
压缩成型
- 过程: 将预热的橡胶放入模腔中,然后在热和压力下成型。材料在模具中固化,形成最终部件。
- 最适合: 生产量低至中等,零件复杂程度简单至中等,材料固化时间较长(如硅胶)。
- 优点: 降低工具成本,可生产大型、厚的零件。
- 缺点: 循环时间较长,复杂形状的精度较低。
吹塑
- 过程: 利用加压空气在模具内膨胀空心型坯,并在冷却时成型橡胶。
- 最适合: 空心部件,如橡胶瓶或囊袋。
- 优点: 可有效制作空心物品。
- 缺点: 仅限于空心形状,可能缺乏尺寸精度。
旋转成型
- 过程: 将一定量的橡胶加热并放入模具中旋转,利用离心力均匀地涂覆内部并形成空心部件。
- 最适合: 大型空心部件,例如容器或汽车零部件。
- 优点: 壁厚均匀,对于大型物件来说很经济。
- 缺点: 循环时间较慢,仅限于空心设计。
液体注射成型 (LIM)
- 过程: 将液态硅橡胶 (LSR) 注入模具,加热并固化。此工艺通常使用双组分液态硅树脂进行快速固化。
- 最适合: 大批量生产精密零件,包括医疗和食品级应用。
- 优点: 精度高,循环时间快,适用于复杂零件。
- 缺点: 需要专门的设备和材料。
挤压成型
- 过程: 橡胶被迫通过模具形成管材或型材等连续的形状,然后硫化(固化)以保持形状。
- 最适合: 连续长度的橡胶制品,例如软管、垫圈和密封件。
- 优点: 适合长而均匀的形状,支持连续生产。
- 缺点: 仅限于较简单的形状,成型后需要切割或修整。
真空成型
- 过程: 将橡胶放入密封模具中,真空抽走空气,确保橡胶充满模腔。然后加热固化材料。
- 最适合: 复杂的部件中存在令人担心的空气滞留问题。
- 优点: 减少气泡等缺陷,产生更好的表面光洁度。
- 缺点: 过程较慢,需要专门的设备。
每种橡胶成型技术都具有独特的优势,具体取决于零件设计、材料特性、生产量和成本。选择正确的工艺可确保特定应用获得最佳效果。
获取报价
请告知我们如何回复您。