Die Enbi Group, ein führender Anbieter industrieller Polyurethan-Rollenlösungen für verschiedene Branchen, hat enge Kooperationen mit führenden OEMs und Hauptlieferanten auf der ganzen Welt aufgebaut. Zentraler Bestandteil unseres Ethos ist die Überzeugung, dass die Führungsposition im Rollensektor untrennbar mit der Qualität unserer Komponenten verbunden ist. Unser Fachwissen reicht von der innovativen Polyurethanverarbeitung bis zur Rollenherstellung und den damit verbundenen Technologien.
Wir bedienen eine globale Kundschaft und garantieren durch unsere weitreichende internationale Präsenz eine zuverlässige Lieferkette. Von unserem nordamerikanischen Hub aus versenden wir auf alle großen Kontinente. Wir setzen uns konsequent für Fortschritt ein und investieren in modernste Ausrüstung und Techniken, um unser Engagement für Qualität, schnelle Lieferung und Effektivität aufrechtzuerhalten. Dies ist das Markenzeichen von Enbi für Überlegenheit und Führung – die Bedürfnisse unserer Kunden stehen immer an erster Stelle.
Polyurethanrollen sind äußerst vielseitige Komponenten, die in verschiedenen industriellen Anwendungen eingesetzt werden. Diese Rollen bestehen aus einem langlebigen Material namens Polyurethan, das hervorragende physikalische Eigenschaften wie Reißfestigkeit, Elastizität und Tragfähigkeit bietet. Mit einer breiten Palette an Härtegraden können Polyurethanrollen an spezifische Anforderungen angepasst werden, wodurch enge Toleranzen und ein reibungsloser Betrieb gewährleistet werden.
Polyurethanrollen sind ideal für schwere Lasten und anspruchsvolle Umgebungen, ob als Umlenkrollen und Spannrollen, ob als Umlenkrollen, Vorschubrollen, Führungsrollen oder Spannrollen. Ihre Abriebfestigkeit und ihr leiser Betrieb machen sie zu einer kostengünstigen Lösung mit langer Lebensdauer. Unternehmen wie Meridian-Labor zeichnen sich durch erfahrene Mitarbeiter und Engagement für Produktqualität bei der Herstellung von Polyurethan-Walzen aus.
Verschiedene Urethanräder und kundenspezifische Rollenoptionen bieten die perfekte Lösung für jede industrielle Anwendung. Für weitere Informationen können sich potenzielle Kunden direkt an Meridian Laboratory wenden, um ihre spezifischen Anforderungen zu besprechen und die richtige Polyurethanrolle für ihre Anforderungen zu finden.
Arten von Polyurethan-Rollen
Polyurethan-Rollen gibt es in verschiedenen Ausführungen, die jeweils für bestimmte Anwendungen konzipiert sind. Maßgefertigte Polyurethan-Rollen sind auf besondere Anforderungen wie hohe Belastungen und enge Toleranzen zugeschnitten. Gerade Rollen sind ideal für Branchen, in denen Präzision entscheidend ist, während Sanduhrrollen eine erhöhte Reißfestigkeit und hervorragende elastische Eigenschaften bieten.
Polyurethanwalzen können mit verschiedenen Materialien verbunden werden, darunter Stahl, Aluminium und Fiberglas. Diese Vielseitigkeit macht sie für verschiedene industrielle Anwendungen geeignet, von medizinischen Geräten bis hin zu Spannwalzen. Urethan-Andruckwalzen sorgen für einen leisen Betrieb, während Polyurethan-Zuführwalzen eine kostengünstige Lösung mit langer Lebensdauer bieten.
Polyurethanrollen sind in vielen Härtegraden erhältlich und erfüllen spezifische Anforderungen. Polyurethan ist für viele Branchen ideal, von weichen Rollen für empfindliche Anwendungen bis hin zu abriebfesten Rollen für den Schwerlasteinsatz.
Zusammenfassend lässt sich sagen, dass Polyurethan-Rollen in verschiedenen Ausführungen erhältlich sind, darunter Sonderanfertigungs-, gerade, Sanduhr- und Vorschubrollen. Sie können mit Stahl, Aluminium und Glasfaser verbunden werden, wodurch sie für verschiedene Anwendungen geeignet sind. Polyurethan-Rollen sind aufgrund ihrer Haltbarkeit und Vielseitigkeit in vielen Branchen die bevorzugte Wahl.
Sanduhr-, Vorschub-, Spann- und Führungsrollen aus Urethan
Urethanwalzen sind für die hohen Anforderungen verschiedener Industrieanwendungen konzipiert. Eine solche Sonderwalze ist die Urethan-Sanduhrwalze, deren einzigartige Form eine effizientere Materialhandhabung ermöglicht. Diese Walzen werden häufig in Zuführwalzenanwendungen eingesetzt, wo sie außergewöhnliche Traktion und Griffigkeit bieten und so eine reibungslose und gleichmäßige Materialzufuhr gewährleisten.
Darüber hinaus spielen Urethan-Umlenkrollen eine wichtige Rolle in Fördersystemen, da sie den bewegten Materialien Halt und Führung bieten. Dank ihrer Fähigkeit, hohen Belastungen standzuhalten und eine ausgezeichnete Reißfestigkeit zu zeigen, gewährleisten diese Rollen eine lange Haltbarkeit und zuverlässige Leistung.
Darüber hinaus werden kundenspezifische Führungsrollen häufig in Branchen wie der Druck-, Verpackungs- und Textilherstellung eingesetzt, da sie Materialien präzise ausgerichtet durch die Prozesse führen und so vor Fehleinzügen oder Beschädigungen schützen.
Sanduhr-, Vorschub-, Spann- und Führungsrollen aus Urethan sind eine vielseitige Lösung, die verbesserte Funktionalität und Effizienz in einem breiten Spektrum industrieller Vorgänge bietet.
Die Vielseitigkeit von Urethanwalzen
Sanduhr-, Vorschub-, Umlenk- und Führungsrollen aus Urethan sind vielseitig und können in verschiedenen industriellen Anwendungen eingesetzt werden. Diese Rollen sind für schwere Lasten und enge Toleranzen ausgelegt und eignen sich daher ideal für Anwendungen, bei denen Präzision entscheidend ist.
Einer der Hauptvorteile von Sanduhr-, Zuführ-, Spann- und Führungsrollen aus Urethan ist ihre Reißfestigkeit und ihre elastischen Eigenschaften. Dadurch wird sichergestellt, dass die Rollen den Belastungen des täglichen Gebrauchs standhalten, ohne vorzeitigen Verschleiß oder Beschädigungen zu erleiden.
Sanduhr-, Zuführ-, Umlenk- und Führungsrollen aus Urethan werden häufig in der Fertigung, im Druck, bei Verpackungen und bei der Materialhandhabung verwendet. Sie transportieren Materialien, führen Produkte durch Produktionslinien und unterstützen Fördersysteme.
Diese Rollen sind in vielen verschiedenen Größen und Härtegraden erhältlich und können so an die spezifischen Anforderungen jeder Anwendung angepasst werden. Darüber hinaus sind sie leise im Betrieb und erfordern nur minimale Wartung, was sie auf lange Sicht zu einer kostengünstigen Wahl macht.
Zusammenfassend lässt sich sagen, dass Urethan-Sanduhr-, Vorschub-, Spann- und Führungsrollen vielseitige Komponenten sind, die in verschiedenen industriellen Anwendungen eingesetzt werden. Ihre Fähigkeit, schwere Lasten zu bewältigen, enge Toleranzen einzuhalten und Reißfestigkeit und elastische Eigenschaften zu bieten, machen sie zu einer idealen Wahl für verschiedene Branchen.
Tragfähigkeit von Urethanrollen
In Bezug auf die Tragfähigkeit sind Sanduhr-, Vorschub-, Umlenk- und Führungsrollen aus Polyurethan für ihre außergewöhnliche Festigkeit bekannt. Diese Rollen sind für die problemlose Handhabung schwerer Lasten konzipiert und daher eine zuverlässige Wahl für verschiedene industrielle Anwendungen.
Meridian Laboratory, ein führender Hersteller in der Branche, bietet ML6-Präzisions-Antriebsrollen mit Polyurethan-Gummibeschichtung an, die sich durch hervorragende Tragfähigkeit auszeichnen. Diese Rollen sind in verschiedenen Größen erhältlich und können an spezifische Anforderungen angepasst werden. Dank ihrer robusten Konstruktion können sie erhebliches Gewicht tragen, ohne die Leistung zu beeinträchtigen.
Zusätzlich zu den ML6-Rollen bietet Meridian Laboratory kostengünstige, individuell geformte Polyurethan-Rollen an. Diese Rollen können in Größe und Profil maßgeschneidert werden, sodass sie für jede Anwendung optimal geeignet sind. Dank der großen Auswahl an Optionen können Kunden die für ihre spezifischen Anforderungen am besten geeignete Tragfähigkeit und Ausführung auswählen.
Die Sanduhr-, Zuführ-, Spann- und Führungsrollen von Meridian Laboratory sind hinsichtlich ihrer Tragfähigkeit zuverlässig. Diese Rollen sind für hohe Belastungen ausgelegt und bieten die in industriellen Umgebungen erforderliche Haltbarkeit und Festigkeit. Durch das Angebot von ML6-Präzisions-Antriebsrollen mit Polyurethan-Gummibeschichtung und kostengünstigen, individuell geformten Optionen stellt Meridian Laboratory sicher, dass seine Kunden Zugang zu den besten Tragfähigkeitslösungen haben.
Reißfestigkeit und elastische Eigenschaften für schwere Lasten und enge Toleranzen
Polyurethan-Rollen von Meridian Laboratory sind so konstruiert, dass sie eine außergewöhnliche Reißfestigkeit und Elastizität aufweisen, wodurch sie sich ideal für die Handhabung schwerer Lasten und den Betrieb innerhalb enger Toleranzen eignen. Diese Rollen sind so konzipiert, dass sie den anspruchsvollen Bedingungen standhalten, die häufig in industriellen Anwendungen auftreten.
Dank ihrer bemerkenswerten Haltbarkeit und Zuverlässigkeit können sie schwere Lasten effektiv tragen, ohne Kompromisse bei der Leistung einzugehen. Die Reißfestigkeit der Polyurethanrollen sorgt für eine längere Lebensdauer und minimiert den Bedarf an häufigen Austauschvorgängen.
Darüber hinaus behalten diese Rollen aufgrund ihrer elastischen Eigenschaften ihre ursprüngliche Form und Leistung unter Druck bei. Daher eignen sie sich hervorragend für Anwendungen, die eine präzise Steuerung und enge Toleranzen erfordern.
Ob beim Umgang mit schweren Lasten oder beim Betrieb in Umgebungen mit engen Toleranzen: Die Polyurethan-Rollen von Meridian Laboratory bieten eine zuverlässige Lösung, die Reißfestigkeit und elastische Eigenschaften für optimale Leistung vereint.
Hohe Reißfestigkeit und elastische Eigenschaften durch hochwertige Materialien
Aufgrund ihrer außergewöhnlichen physikalischen Eigenschaften werden Polyurethanrollen häufig in verschiedenen industriellen Anwendungen eingesetzt. Ein Schlüsselfaktor, der zu ihrer Leistung und Haltbarkeit beiträgt, ist die Verwendung hochwertiger Materialien.
Durch die Verwendung hochwertiger Materialien wie Polyurethan in Premiumqualität können Hersteller eine hohe Reißfestigkeit und elastische Eigenschaften ihrer Rollen erreichen. Reißfestigkeit ist bei Anwendungen von entscheidender Bedeutung, bei denen die Rollen hohen Belastungen und engen Toleranzen ausgesetzt sind. Sie stellt sicher, dass die Rollen der Belastung und dem Druck standhalten können, ohne zu reißen oder zu versagen.
Elastische Eigenschaften sind bei Polyurethanrollen ebenfalls von entscheidender Bedeutung, da sie dafür sorgen, dass die Rollen ihre Form behalten und unter verschiedenen Bedingungen zuverlässig funktionieren. Hochwertige Materialien mit hervorragender Elastizität halten wiederholtem Biegen und Verbiegen stand, ohne ihre ursprüngliche Form zu verlieren, was zu einer längeren Lebensdauer und einem zuverlässigen Betrieb führt.
Bei der Auswahl der Materialien für Polyurethanwalzen müssen unbedingt die spezifischen Anwendungsanforderungen berücksichtigt werden. Unterschiedliche Härtegrade, gemessen mit Durometern, können sich auf Reißfestigkeit und Elastizität auswirken. Weiche Durometer bieten eine höhere Reißfestigkeit, während härtere Durometer eine verbesserte Elastizität bieten. Hersteller bieten eine große Auswahl an Durometern, sodass Kunden die Leistung ihrer Walzen basierend auf den Anforderungen ihrer spezifischen Anwendungen optimieren können.
Zusammenfassend lässt sich sagen, dass das Erreichen einer hohen Reißfestigkeit und elastischer Eigenschaften bei Polyurethanrollen in hohem Maße von der Verwendung hochwertiger Materialien abhängt. Durch die Auswahl des richtigen Materials und Härtegrads für die vorgesehene Anwendung können Hersteller sicherstellen, dass ihre Rollen hohen Belastungen und engen Toleranzen standhalten und eine zuverlässige und langlebige Lösung bieten.
Vielfältige industrielle Einsatzmöglichkeiten für gerade Walzen, Metall-, Gummi- und Ersatzwalzen
Polyurethanrollen haben verschiedene industrielle Anwendungen, z. B. als gerade Rollen, Metallrollen, Gummirollen und Ersatzrollen. Gerade Rollen werden häufig in Fördersystemen verwendet, um die Bewegung von Waren und Materialien zu erleichtern. Metallrollen bieten eine hervorragende Tragfähigkeit und sind ideal für Schwerlastanwendungen. Gummiwalzen bieten eine weichere Oberfläche für empfindliche Materialien und werden häufig in der Druck- und Papierverarbeitungsindustrie verwendet. Ersatzrollen sind kostengünstig, um abgenutzte oder beschädigte Rollen in verschiedenen Geräten und Maschinen zu ersetzen. Von der Herstellung und Verpackung bis hin zum Druck und Materialtransport sind Polyurethanrollen aufgrund ihrer Vielseitigkeit für eine breite Palette industrieller Anwendungen geeignet. Ihre Haltbarkeit, Reißfestigkeit und elastischen Eigenschaften machen sie in vielen Branchen beliebt, darunter Automobil-, Pharma-, Lebensmittelverarbeitung und mehr.
Passende Walze für Ihre Anwendungsanforderungen
Bei der Auswahl der richtigen Walze für Ihre spezifischen Anwendungsanforderungen ist es wichtig, die unterschiedlichen Eigenschaften und Verwendungsmöglichkeiten der verschiedenen Walzenmaterialien zu verstehen. Drei gängige Walzenmaterialien sind Nylon, Polyurethan und Stahl.
Nylonrollen sind für ihre hohe Festigkeit und Haltbarkeit bekannt. Sie bieten eine ausgezeichnete Abriebfestigkeit und werden häufig in Anwendungen eingesetzt, die hohe Lasten und enge Toleranzen erfordern. Nylonrollen findet man häufig in Fördersystemen, Zuführrollen und Führungsrollen.
Polyurethanrollen sind vielseitig und bieten eine breite Palette physikalischer Eigenschaften. Sie sind für ihre Reißfestigkeit und Elastizität bekannt und eignen sich daher ideal für verschiedene industrielle Anwendungen. Polyurethanrollen können individuell an Härtebereiche, Tragfähigkeit und Außendurchmesser angepasst werden. Sie werden häufig in der Fertigung, in der Medizintechnik und in der Produkthandhabung eingesetzt.
Stahlrollen sind für ihre Stärke und Tragfähigkeit bekannt. Sie werden häufig in Anwendungen eingesetzt, die hohe Anforderungen an die Leistung stellen, wie z. B. im Bergbau, im Bauwesen und in der Materialhandhabungsindustrie. Stahlrollen halten hohen Belastungen stand und bieten eine lange Lebensdauer.
Um die richtige Rolle für Ihre Anwendungsanforderungen zu finden, müssen die spezifischen Eigenschaften jedes Materials berücksichtigt werden. Technische Daten wie Härtegrade, Abriebverlust und Tragzahlen sind für die Auswahl des geeigneten Rollenmaterials von entscheidender Bedeutung. Wenn Sie die unterschiedlichen Eigenschaften und Verwendungsmöglichkeiten von Rollen aus Nylon, Polyurethan und Stahl kennen, können Sie sicherstellen, dass Sie die für Ihre spezifischen Anwendungsanforderungen am besten geeignete Rolle auswählen.
Mit der richtigen Materialwahl eine dauerhafte Produktqualität sicherstellen
Die Auswahl des richtigen Materials für Polyurethanrollen gewährleistet eine dauerhafte Produktqualität. Die Materialauswahl hat großen Einfluss auf die Leistung und Langlebigkeit der Rollen in verschiedenen industriellen Anwendungen.
Polyurethan ist aufgrund seiner zahlreichen Vorteile gegenüber anderen Materialien wie Kunststoff, Gummi und Metall ein hervorragendes Rollenmaterial. Polyurethan bietet eine außergewöhnliche Schlag- und Abriebfestigkeit und eignet sich daher hervorragend für Schwerlastanwendungen. Es hält den schwierigsten Bedingungen stand, ohne sich abzunutzen oder seine Funktionalität zu verlieren.
Darüber hinaus weist Polyurethan eine bemerkenswerte Flexibilität, Reißfestigkeit und einen großen Härtebereich auf. Dadurch können maßgeschneiderte Rollen spezifische Anforderungen erfüllen und bei unterschiedlichen Tragfähigkeiten optimale Leistung erbringen. Die Vielseitigkeit von Polyurethan macht es zur idealen Wahl für eine Vielzahl von Anwendungen, darunter Fertigung, medizinische Geräte und Produkthandhabung.
Unternehmen können eine dauerhafte Produktqualität sicherstellen, indem sie diese Schlüsselfaktoren sorgfältig berücksichtigen und Polyurethan als Material für Rollen auswählen. Polyurethanrollen bieten dauerhafte Leistung, geringere Wartungskosten und eine längere Lebensdauer als andere Materialien. Dies wiederum erhöht die Produktivität und Effizienz in industriellen Prozessen.
Zusammenfassend lässt sich sagen, dass die Auswahl des richtigen Materials, wie z. B. Polyurethan, entscheidend ist, um eine dauerhafte Produktqualität für Polyurethanwalzen sicherzustellen. Seine bemerkenswerten Vorteile gegenüber Kunststoff, Gummi und Metall, darunter Schlag- und Abriebfestigkeit, Flexibilität, Reißfestigkeit und ein breites Härtespektrum, machen es zur idealen Wahl für verschiedene Anwendungen.
Physikalische Eigenschaften von Polyurethanwalzen
Polyurethan-Rollen sind für ihre außergewöhnlichen physikalischen Eigenschaften bekannt, was sie in vielen Branchen zur bevorzugten Wahl macht. Eine bemerkenswerte Eigenschaft ist ihre herausragende Haltbarkeit, die selbst unter anspruchsvollen Bedingungen eine lange Lebensdauer gewährleistet. Diese Rollen weisen eine hohe Abriebfestigkeit auf, sodass sie ständiger Abnutzung standhalten können, ohne dass die Leistung beeinträchtigt wird. Darüber hinaus verhindert ihre Reißfestigkeit, dass sie selbst bei schwerer Belastung leicht reißen oder brechen.
Polyurethanrollen zeichnen sich durch ihre beeindruckende Tragfähigkeit aus. Unabhängig vom Gewicht oder Druck können diese Rollen schwere Lasten effektiv tragen und sorgen für einen zuverlässigen und stabilen Betrieb.
Ein weiterer bemerkenswerter Vorteil von Polyurethanwalzen ist ihre Fähigkeit, sich mit verschiedenen Materialien zu verbinden. Ob Stahl, Aluminium oder Fiberglas, Polyurethan kann eine starke Verbindung mit diesen Substraten eingehen und so eine sichere und zuverlässige Verbindung gewährleisten. Diese Vielseitigkeit ermöglicht die Herstellung verschiedener Walzen, darunter Stufen- und Tauchwalzen, Förderwalzen, Andruckwalzen und Umlenkwalzen, die auf spezifische industrielle Anforderungen zugeschnitten sind.
Polyurethanrollen bieten große Vielseitigkeit in Produktionslinien und finden Anwendung in verschiedenen Branchen. Ihre physikalischen Eigenschaften wie Haltbarkeit, Abriebfestigkeit, Reißfestigkeit und Tragfähigkeit machen sie unverzichtbar für Aufgaben mit schweren Lasten und rauen Umgebungen. Diese Rollen bieten einen zuverlässigen und präzisen Betrieb und gewährleisten optimale Leistung und Produktivität.
Insgesamt sind Polyurethan-Walzen aufgrund ihrer physikalischen Eigenschaften, ihrer Fähigkeit, sich an unterschiedliche Materialien zu binden, und der Vielfalt der verfügbaren Typen die ideale Wahl für zahlreiche Anwendungen, von Industriemaschinen bis hin zu Produktionslinien in verschiedenen Branchen.
Gängige Anwendungen von Polyurethan-Walzen
Polyurethanrollen werden aufgrund ihrer Langlebigkeit, Abriebfestigkeit und Verfügbarkeit in verschiedenen Größen in verschiedenen Branchen häufig eingesetzt. Diese Eigenschaften machen sie äußerst vielseitig und ideal für verschiedene Anwendungen.
In Produktionslinien werden Polyurethanrollen häufig für Fördersysteme verwendet. Sie halten schweren Lasten stand und sorgen für eine reibungslose und effiziente Bewegung von Materialien. Diese Rollen sind auf Langlebigkeit ausgelegt und gewährleisten eine lange Lebensdauer und minimale Ausfallzeiten.
Polyurethanrollen werden auch häufig in Antriebssystemen verwendet. Sie sorgen für eine zuverlässige Kraftübertragung und einen reibungslosen Betrieb, selbst unter anspruchsvollen Bedingungen. Aufgrund ihrer Widerstandsfähigkeit gegen Abriebschäden eignen sie sich für Hochgeschwindigkeitsanwendungen und Schwerlastaufgaben.
Darüber hinaus werden Polyurethanrollen häufig als Umlenkrollen eingesetzt. Sie führen und stützen Förderbänder und sorgen für eine zuverlässige und effiziente Bewegung. Aufgrund ihrer Langlebigkeit und Verschleißfestigkeit sind sie ideal für den Dauerbetrieb in der Fertigungs-, Logistik- und Bergbauindustrie.
Eine weitere häufige Anwendung für Polyurethan-Rollen sind Zuführrollen. Sie werden verwendet, um den Materialfluss in Maschinen zu bewegen und zu steuern und so eine präzise und gleichmäßige Zuführung zu gewährleisten. Aufgrund ihrer Langlebigkeit sind Polyurethan-Rollen eine zuverlässige Wahl für Zuführsysteme in verschiedenen Branchen, wie z. B. Druck, Verpackung und Materialhandhabung.
Insgesamt sind Polyurethanrollen unverzichtbare Komponenten in Produktionslinien und industriellen Prozessen. Aufgrund ihrer Haltbarkeit, Abriebfestigkeit und Verfügbarkeit in verschiedenen Größen eignen sie sich für verschiedene Anwendungen, darunter Fördersysteme, Antriebssysteme, Umlenkrollen und Vorschubrollen.
Kundenspezifische Polyurethan-Rollen
Maßgefertigte Polyurethanrollen sind vielseitige Komponenten, die an die spezifischen Anforderungen verschiedener Branchen angepasst werden können. Maßgefertigte Polyurethanrollen bieten eine zuverlässige und effiziente Lösung, egal ob für schwere Lasten, enge Toleranzen oder spezifische physikalische Eigenschaften. Da diese Rollen in verschiedenen Größen, Formen und Härtegraden hergestellt werden können, können sie an eine Vielzahl von Anwendungen angepasst werden.
Maßgefertigte Polyurethanrollen bieten optimale Tragfähigkeit und außergewöhnliche Reißfestigkeit und sind daher ideal für anspruchsvolle Industrieanwendungen. Ihr langlebiges Material und ihre elastischen Eigenschaften sorgen für eine lange Lebensdauer und einen leisen Betrieb. Bei maßgefertigten Polyurethanrollen gibt es endlose Möglichkeiten. Mit Hilfe erfahrener Mitarbeiter und fortschrittlicher Herstellungsverfahren ist die Herstellung dieser Rollen effizient und kostengünstig.
Entwicklung und Herstellung kundenspezifischer Polyurethan-Rollen
Die Entwicklung und Herstellung kundenspezifischer Polyurethanrollen erfordert akribische Liebe zum Detail und Fachwissen im Umgang mit den physikalischen Eigenschaften von Rädern aus massivem Polyurethan und gegossenem Urethan. Diese Rollen werden in verschiedenen Anwendungen eingesetzt, von der Schwerlastbeanspruchung bis zur präzisen Spannungsregelung.
Der Prozess beginnt mit der Konstruktion der Rolle, um spezifische Anforderungen zu erfüllen. Dazu gehört die Bestimmung der genauen Abmessungen, der Tragfähigkeit und des gewünschten Härtebereichs. Die Härte wird mit der Shore-Härteskala Durometer gemessen, und eine enge Toleranz von +/- 0,005 stellt sicher, dass die Rollen die genauen Spezifikationen erfüllen.
Sobald das Design fertig ist, werden Räder aus massivem Polyurethan oder gegossenem Urethan mit Metallnaben hergestellt. Massive Polyurethanrollen sind ideal für Anwendungen, bei denen Reißfestigkeit und hohe Tragzahlen erforderlich sind. Räder aus gegossenem Urethan mit Metallnaben bieten erhöhte Festigkeit und Haltbarkeit.
Kundenspezifische Polyurethanwalzen können in verschiedenen Typen hergestellt werden, z. B. als Stufen- und Tauchwalzen, Chevron- und Quetschwalzen. Jeder Typ dient je nach Anwendung einem bestimmten Zweck. Stufen- und Tauchwalzen führen Materialien durch einen Prozess, Chevron-Walzen ermöglichen eine reibungslose Bewegung auf geneigten Oberflächen und Quetschwalzen gewährleisten optimalen Kontakt bei Bahnhandhabungsvorgängen.
Ein Vorteil der Zusammenarbeit mit erfahrenen Herstellern ist die Möglichkeit, maßgeschneiderte Polyurethan-Rollen schnell zu liefern. Dies minimiert Ausfallzeiten und gewährleistet einen schnellen Austausch oder eine schnelle Installation.
Die Entwicklung und Herstellung kundenspezifischer Polyurethan-Rollen erfordert Fachwissen, Präzision und die Fähigkeit, qualitativ hochwertige Produkte herzustellen. Ob für schwere Industrieaufgaben oder medizinische Geräte, diese Rollen bieten kostengünstige und langlebige Lösungen für verschiedene Anwendungen. Bitte wenden Sie sich an unser erfahrenes Personal, um mehr über unsere verschiedenen kundenspezifischen Polyurethan-Rollen zu erfahren und wie sie Ihren Betrieb unterstützen können.
Vorteile von maßgefertigten Polyurethan-Rollen
Maßgefertigte Polyurethanrollen bieten eine Reihe von Vorteilen, die sie zur idealen Wahl für verschiedene industrielle Anwendungen machen. Diese Rollen können so entworfen und hergestellt werden, dass sie den Anforderungen der Industrie entsprechen und so eine verbesserte Leistung, längere Lebensdauer und Kosteneffizienz gewährleisten.
Bei der Entwicklung kundenspezifischer Polyurethanrollen berücksichtigen die Hersteller die genauen Abmessungen, die Tragfähigkeit und den gewünschten Härtebereich. Dadurch können maßgeschneiderte Rollen für die jeweilige Anwendung hergestellt werden. Diese Rollen erfüllen präzise Spezifikationen, indem die Härte mit der Shore-Härteskala von Durometer gemessen wird und enge Toleranzen von +/- 0,005 eingehalten werden.
Ein Typ von Sonderwalze, der die Vielseitigkeit von Polyurethan demonstriert, ist die Urethan-Sanduhrwalze. Diese Walzen haben eine einzigartige Form, die eine effizientere Materialhandhabung ermöglicht. Sie werden häufig in Zuführwalzenanwendungen eingesetzt, da sie hervorragende Traktion und Griffigkeit bieten und eine reibungslose und gleichmäßige Materialzufuhr gewährleisten.
Eine andere Art von Sonderrollen ist die Urethan-Umlenkrolle. Diese Rollen werden häufig in Fördersystemen verwendet und bieten Unterstützung und Führung für bewegte Materialien. Sie sind für hohe Belastungen ausgelegt und weisen eine hervorragende Reißfestigkeit auf, wodurch eine lange Haltbarkeit gewährleistet wird.
Auch kundenspezifische Führungsrollen sind in verschiedenen Branchen beliebt, darunter Druck, Verpackung und Textilherstellung. Diese Rollen führen Materialien durch Prozesse, sorgen für eine präzise Ausrichtung und verhindern Fehleinzüge oder Beschädigungen.
Zu den Vorteilen maßgeschneiderter Polyurethan-Rollen gehören eine verbesserte Leistung aufgrund ihres präzisen Designs, eine längere Lebensdauer dank ihrer Strapazierfähigkeit und Reißfestigkeit sowie Kosteneffizienz durch reduzierte Ausfallzeiten und Wartungsaufwand. Ihre Vielseitigkeit und Fähigkeit, spezifische Branchenanforderungen zu erfüllen, machen sie zur bevorzugten Wahl für viele Anwendungen.
Häufig gestellte Fragen
Wie erfolgt die Herstellung von Polyurethan-Walzen?
Der Herstellungsprozess umfasst das Mischen zweier flüssiger Komponenten, eines Polyols und eines Isocyanats. Diese Mischung wird in eine Form gegossen und erhitzt, um eine feste Struktur zu erzeugen. Anschließend wird sie geformt und poliert, um die Walzen herzustellen.
Gibt es im Zusammenhang mit der Herstellung oder Entsorgung von Polyurethan-Walzen Umweltbedenken?
Ja, bei der Herstellung und Entsorgung von Polyurethanwalzen bestehen Umweltbedenken. Bei der Herstellung werden Chemikalien verwendet, die potenziell umweltschädlich sind. Auch die Entsorgung kann problematisch sein, da Polyurethan nicht leicht biologisch abbaubar ist. Richtige Abfallbewirtschaftungsstrategien sind unerlässlich.
Können Urethanwalzen nach Gebrauch recycelt oder wiederverwendet werden?
Ja, Recycling oder Wiederverwendung sind für viele Produkte möglich, abhängig vom jeweiligen Materialtyp. Für Polyurethanwalzen kann es zwar eine Herausforderung sein, aber es gibt einige Recyclingverfahren.
Wie sind die Kosten von Polyurethanrollen im Vergleich zu anderen Materialoptionen?
Zwar sind die Anschaffungskosten von Polyurethan-Rollen möglicherweise höher als bei anderen Materialien wie Gummi oder Kunststoff, aufgrund ihrer Haltbarkeit und des geringeren Wartungsaufwands erweisen sie sich auf lange Sicht jedoch häufig als kostengünstiger.
Gibt es für Polyurethan-Walzen besondere Wartungs- und Reinigungsanforderungen?
Für diese Walzen gibt es keine besonderen Wartungs- oder Reinigungsanforderungen. Regelmäßige Reinigung mit einem feuchten Tuch und einem milden Reinigungsmittel wird empfohlen. Um die Haltbarkeit zu erhalten, sollten sie trocken und vor extremen Temperaturen geschützt aufbewahrt werden.
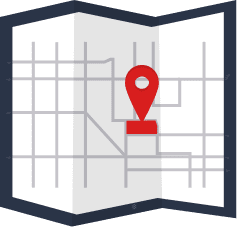
Finden Sie Ihre lokale Enbi-Niederlassung, um sich nach unseren Laderollen zu erkundigen.

Dringende technische Frage? Lassen Sie sich von unseren erfahrenen Ingenieuren beraten.