1. さまざまな金属を組み合わせる
このプロセスでは、従来の溶接では接合できないさまざまな金属を溶接できます。たとえば、アプリケーションで (高価な) 耐腐食性材料が必要になる場合があります。ただし、コンポーネント全体を耐腐食性にする必要はない場合があります。慣性溶接を使用すると、必要がない場合に耐腐食性材料と耐腐食性の低い材料を組み合わせることができます (もちろん、慣性溶接では類似の金属を組み合わせることもできます)。
2. 高価な材料の必要性を減らす
慣性溶接では、高価な材料の使用量が減るため、品質を犠牲にすることなくコストを大幅に削減できます。
3. 熱影響部(HAZ)を最小限に抑える
摩擦溶接 熱影響部を最小限に抑えます。言い換えれば、材料特性への影響が少なくなり、よりきれいな仕上がりですぐに使用できます (したがって、生産時間が短縮されます)。
4. 強力で気密性の高い結合を実現
慣性溶接は、断面の表面全体が両方の金属で構成されるように材料を接合します。2 つの金属の機械的な混合と凝固は堅牢で気密性が高く、空隙や多孔性がありません。
従来の溶接と比較した慣性摩擦溶接の利点
1. サイクルタイムの大幅な短縮
摩擦溶接プロセスを使用することでサイクルタイムがどれだけ大幅に短縮されるかは、強調しすぎることはありません。
– 機械制御プロセス
溶接を制御する上で重要な要素 (回転速度、フライホイールの質量、および推力) は機械で制御されるため、MIG 溶接プロセスや TIG 溶接プロセスとは異なり、製品間のばらつきは最小限 (またはまったく) になります。
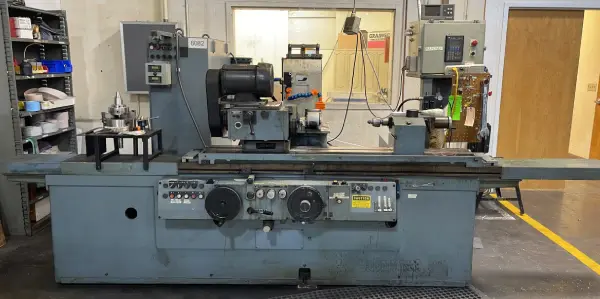
– 極めて高い一貫性と再現性
これらの要素が決定されると (経験豊富な溶接工にとっては迅速なプロセス)、プロセスをほとんど中断することなくコンポーネントを迅速に再現できるため、ほぼすべてのプロジェクトで極めて高い一貫性と再現性が実現します。
– コンポーネントの準備は最小限
最小限に準備された鋸切断面は、プラスチック金属の変位によって元の表面状態が除去され、溶接領域から汚染物質が排出されるため、慣性摩擦溶接プロセスに適しています。
– 溶接後の機械加工は最小限で済みます
ピック 慣性摩擦溶接 この技術により、最小限の後加工でほぼネットシェイプの部品が製造されます。場合によっては、接合部のフラッシュメタルのリングを除去する必要があります。
– 全体的な処理時間の短縮
簡単に言えば、慣性摩擦溶接プロセスは、従来の溶接や機械加工技術に比べてそれほど時間がかかりません。
2. 異種金属の接合
通常、2 つの異なる金属 (ステンレス鋼とアルミニウム、銅と鋼など) の融点に大きな差があるため、従来の技術では溶接が不可能であり、何らかの機械的な接続が必要になります。
慣性摩擦溶接プロセスでは、向かい合う表面を溶かす必要がないため、ワークピースが可塑化され、一緒に押し付けられ、その後冷却されると(隣接する加熱されていない金属がヒートシンクのように機能して)、金属は材料の合金化なしに高整合性の結合を形成します。
部品に異なる金属を選択できるため、製造業者は、高価な金属を必要としないワークピースの部分では高価な金属の使用を排除できます。
これにより、溶接プロセスの材料コストが削減されるだけでなく、重い材料の負担が軽減されるため、アプリケーションの効率的な実行にも役立ちます。
3. 従来の溶接やCNC加工に比べてコスト削減
慣性摩擦溶接プロセスにより、労働時間と材料コストの両方で大幅な節約が実現します。
– 異種金属は節約につながる
前述のように、異種金属を利用できると、部品全体に高価な金属を使用する必要がなくなり、メーカーは材料コストを節約できます。
– 材料費の削減、加工費の削減
このプロセスでは、他の方法で形成された部品と同じ疲労およびトルクしきい値を達成するために必要な原材料が少なくなります。つまり、原材料コストと、余分な材料を除去するための溶接後の機械加工時間の両方が削減されます。
– 廃材を最小限に抑える
CNC 旋盤で製造された部品と比較すると、慣性摩擦溶接では材料の廃棄がほとんどまたはまったく発生しないため、メーカーは同じ生産量を達成するために購入する材料を大幅に削減できます。
– 運用コストの削減
溶融溶接法で必要なガス、充填材、フラックスが不要になるため、コストが削減されます。また、工具コストが下がり、生産性が向上するため、加工コストも削減されます。
4. 高い溶接品質
慣性摩擦溶接は、ガスの多孔性やスラグの混入の可能性がない固体溶接プロセスです。
摩擦溶接は接触領域の 100% 結合を形成し、鍛造結合と同等の品質の接合部を作成します。溶接特性は、MIG 溶接や TIG 溶接などの従来の溶融プロセスで作成された溶接よりも優れています。
このプロセスにより、最終的に親材料と同等かそれ以上の接合強度が実現します。
5. 数量制限なし
慣性摩擦溶接は、進行中のプロジェクトでプロトタイプ、少量生産、または大量繰り返し生産を行うためのコスト効率の高いソリューションです。
6. 労働者の安全
危険な明るい光や溶融物質の飛び散りを排除することで、床上での怪我のリスクが大幅に減少します。
慣性摩擦溶接の最適な使用方法
慣性摩擦溶接は、金属やその他の材料を接合する非常に便利でコスト効率の高い方法ですが、すべての用途に適しているわけではなく、次のようないくつかの制限があります。
- 材料は高温でも展性がある必要がある
- 構造内に脆い相が存在すると制限が生じる(例えば、グラファイト、硫化マンガン、遊離鉛、テルルなどの材料)。
- 鋳鉄は溶接可能な材料のリストから除外されている
- 青銅と真鍮は、鉛含有量が高い場合(> 0.3%)はリストから除外されます。
- 溶接部品の角度方向は現時点では実現不可能である
- 基本的な接合は突合せ溶接でなければならない
- 一般的に、少なくとも1つの部品の接合面は、基本的に円形でなければなりません。
詳細についてはこのガイドをお読みください 慣性摩擦溶接の仕組み.
慣性摩擦溶接のメリットを享受できるアプリケーション
1. ローラー製造
慣性摩擦溶接プロセスにより、工業用ローラーに依存するメーカーのコストとサイクル時間が削減されます。
- ニップ ローラー: ニップ ロールは、2 枚以上のシートをプレスして積層製品を形成するために使用される動力付きロールです。ニップ ポイントで発生する圧力によってシートが接触し、気泡や膨れが押し出されます。
- 給紙ローラー: 枚葉印刷機では、給紙ローラーは紙を積み重ねテーブルからグリッパーに送るゴム製の車輪のセットのうちの 1 つです。
- 熱伝達ローラー: 熱伝達ローラーは、加熱または冷却された流体をロールの外殻の下のコイルに循環させることで温度を制御します。流体はロール表面をアプリケーションに必要な温度まで冷却または加熱します。
- コンベアローラー
- プレッシャー/定着ローラー
2. 掘削と採掘
読む 慣性摩擦溶接の事例研究 天然ガス採掘業界の会社向けに掘削ロッドを作成する。
- 石油掘削
- 天然ガス掘削
- 井戸掘り
3. 高強度金属を必要とする航空宇宙部品
4. 空気圧アセンブリ
慣性摩擦溶接について詳しく知る
慣性摩擦溶接とは何ですか?
慣性摩擦溶接はどのように機能するのでしょうか?
摩擦溶接品質管理プロセス
インターシャフト摩擦溶接の事例