Custom Precision Rollers: Industry-Leading Expertise and Innovation
Precision ROLLERS
Enbi Group partners with leading OEMs and tier-one suppliers worldwide, offering unmatched expertise in precision machining. Our advanced capabilities in inertia welding, roller manufacturing, and forming technologies allow us to deliver custom precision rollers designed to meet your exact needs.
Inertia welding provides significant advantages, including up to 30% savings in waste materials and reductions in roller weight and costs by up to 25%. These benefits not only improve sustainability but also help reduce manufacturing expenses for your business.
With a global presence and dependable supply chain, we serve industries across four continents from our North American headquarters. By investing in state-of-the-art tools and processes, we ensure consistent quality, efficiency, and timely delivery.
Get in touch with our experts today to discuss your project and request a quote, or explore more about our precision roller solutions below.
In the world of manufacturing and industrial applications, precision rollers hold a pivotal role. These specialized tools, as their name suggests, are designed with an emphasis on precision, ensuring streamlined functionality and efficiency in a variety of processes. This article will delve into the world of precision rollers, exploring their design, working principles, and the unmatched importance they hold in the manufacturing sector. We’ll also touch upon the crucial aspects to consider when choosing the right precision roller equipment for your needs, and share some handy tips on its maintenance and care. Whether you’re a seasoned professional in the industry or simply curious about these essential tools, this comprehensive guide will provide a wealth of knowledge on precision rollers. So, let’s roll into the specifics and unravel the intricacies of these indispensable industrial tools.
Understanding the Role of These Tools in Industry
In the bustling world of industry, there’s no denying the critical role precision rollers play, acting as the unseen heroes ensuring smooth operations and fine-tuned processes. These tools, often overlooked, are indispensable in various sectors, such as printing, manufacturing, cash handling, and packaging. Precision rollers ensure accuracy and consistency in production lines, significantly reducing the potential for errors and inefficiencies. Their primary function is to guide and transport materials through the production process. They are designed with exacting standards to handle different types of substances, including paper, plastic, and metal. The use of these rollers is not limited to industrial applications. They are also found in everyday items such as printers, scanners, ATMs and copiers. The impact of precision rollers extends far beyond their physical presence, contributing to the overall efficiency and effectiveness of an operation.
Crafting these cylindrical tools requires an intricate understanding of their design and functioning principles. Precision rollers are meticulously designed to ensure they fulfill their role effectively in various industrial applications. They are typically crafted from robust materials such as steel, aluminium, rubber rollers, silicone, foam, and polyurethane ensuring durability and longevity. The design process involves shaping the roller to exact specifications, with a focus on achieving a smooth, flawless surface with controlled reduce friction and optimal wear.
The functioning principle of precision rollers is relatively simple: they rotate to move or transport materials along a designated path. However, their performance is directly influenced by their design details, such as their dimensions, material selection, coefficient of friction, electrical properties and surface finish. Therefore, accuracy in design and manufacturing is paramount to their effectiveness.
You’d be amazed at how pivotal these cylindrical tools are in various manufacturing processes. Precision rollers are integral to the production line, ensuring efficiency and smooth operation. Their primary function is to minimize friction, allowing objects to move more easily along a path. This reduced resistance greatly enhances speed and productivity.
In industries like printing, paper, and textile, these rollers are indispensable. They ensure uniformity and accuracy in printing, contribute to the efficient production of paper, and the flawless weaving of textiles. Furthermore, in conveyor systems, precision rollers facilitate the seamless transportation of goods, boosting overall productivity.
The importance of precision rollers in manufacturing processes cannot be overstated. Their role in enhancing efficiency, improving speed, and ensuring the quality of output is crucial.
Selecting the Right Equipment for Your Needs
Choosing the right equipment for your manufacturing needs isn’t just about convenience or cost-effectiveness, it’s a critical decision that directly impacts productivity and quality of output. When it comes to precision rollers, several factors need to be assessed. Function, Size, material, speed, substrate being fed and load capacity are all important considerations. The roller’s size should match the specifics of your machinery and products. The material should withstand the environmental conditions of your operation, whether that’s high temperature, corrosive substances, or heavy loads. Load capacity is crucial as it determines the roller’s ability to handle the weight of your products without affecting performance. Consulting with technical experts or suppliers can provide valuable insights to ensure you choose the equipment that best suits your operational requirements.
Maintenance and Care Tips
Once you’ve secured the right equipment, it’s essential to keep it in top-notch condition with regular maintenance and care. Precision rollers are a significant investment, and their longevity depends heavily on how well they are looked after. Regular cleaning is crucial to remove any dust or debris that may accumulate, as this can lead to impairments in the rollers’ function. Lubrication is another important aspect to ensure smooth operation and prevent unnecessary wear and tear. Periodic inspections should be carried out to detect any signs of damage or wear early on, allowing for timely repair or replacement. Proper storage is also pivotal; precision rollers should be stored in a dry, cool place and covered to protect them from potential damage. Following these tips can ensure your equipment performs optimally and lasts longer.
Materials Used in the Manufacture of Rubber Rollers
The materials used in rubber rollers are crucial in determining their performance and suitability for various applications. Rubber rollers are typically made using elastomer compounds, which provide the desired properties such as excellent resistance to wear, heat, and chemicals. These elastomer compounds are applied as a layer on roller cores, often made of materials like stainless steel or rigid composites. The outer layer of elastomer material provides the necessary traction and grip for effective ink distribution in the printing and packaging industries and ensures dimensional stability and durability. Depending on the specific application, different types of rubber can be used to achieve the desired performance characteristics, such as natural rubber, silicone rubber, or synthetic rubber. The use of high-quality materials and advanced manufacturing processes contributes to rubber rollers’ long service life and reliability, making them an integral component in various industrial and commercial sectors.
Natural Rubber
Natural rubber is a versatile and widely used material in various industries, particularly in manufacturing rubber rollers. With its unique characteristics and properties, natural rubber offers excellent heat buildup and fatigue resistance, making it highly desirable for such applications.
One of the key advantages of natural rubber is its exceptional heat resistance. It can withstand high temperatures without deforming or losing its integrity. This makes it ideal for use in industries where heat buildup is common, such as the paper industry. Natural rubber exhibits excellent fatigue resistance, which can withstand repeated stress and strain without experiencing significant wear or damage.
Furthermore, natural rubber’s desirable properties contribute to its effectiveness as a roller cover material. It offers superior dimensional stability, ensuring the roller maintains its shape and performs optimally over its service life. The grooved pattern on the surface of the roller helps with ink distribution and provides better traction. Moreover, natural rubber’s physical characteristics, such as its elasticity and flexibility, allow it to conform to various roller cores and integral shafts.
In summary, natural rubber is an excellent choice for manufacturing rubber rollers due to its heat buildup and fatigue resistance. Its desirable properties, including dimensional stability and ink distribution capabilities, further enhance its functionality in industrial applications.
Layer of Elastomer Compounds (Elastomers)
In the manufacturing process of rubber rollers, a layer of elastomer compounds, known as elastomers, is used to provide the necessary properties and performance characteristics. Ethylene propylene rubber (EPM/EPDM) is a commonly used elastomer compound.
Elastomers like EPM/EPDM are polymerized during manufacturing to achieve desirable characteristics. One of the key benefits is their excellent weathering resistance, which allows the rubber rollers to withstand exposure to outdoor elements without degrading or losing their performance. This makes them suitable for a wide range of industrial applications.
Also, elastomers like EPM/EPDM exhibit superior insulating properties, making them ideal for electrical and electronic industries. They can effectively resist the flow of electric current and provide a protective barrier against electrical hazards.
Moreover, elastomers offer excellent mechanical properties at both high and low temperatures. They can withstand extreme temperature variations without losing their elasticity or flexibility, ensuring optimal performance of the rubber rollers in various environments.
Elastomers can be cured using sulfur or peroxide, enabling the rubber rollers to maintain their shape and integrity during use. This curing process enhances their durability and resistance to physical stress.
Furthermore, elastomers possess good chemical resistance, allowing them to withstand exposure to various chemicals and substances without damage or degradation. This makes them suitable for use in industries where contact with chemicals is common.
In conclusion, the layer of elastomer compounds, such as EPM/EPDM, used in manufacturing rubber rollers provides excellent weathering resistance, insulating properties, and mechanical strength at high and low temperatures. Their ability to be cured and their chemical resistance further enhance the durability and performance of rubber rollers.
Shaft of Stainless Steel or Other Metal Alloy
The core of shaft of rubber rollers is often made of stainless steel or other metal alloys, providing additional strength and protection to the roller. This outer layer acts as a core, offering resistance against external forces and is key for the durability of the roller.
Using stainless steel or other metal alloys in the shaft enhances the durability and longevity of the rubber roller. These materials have excellent tensile strength, allowing the roller to withstand heavy loads and pressures without deformation or failure. They also offer corrosion resistance, ensuring the roller performs even in harsh environments.
Different types of metal alloys are commonly used to manufacture rubber rollers. Stainless steel is a popular choice due to its high durability, corrosion resistance, and ability to maintain its physical properties at various temperatures. Other metal alloys, such as aluminum or rigid material composites, may also be used depending on the specific application requirements.
In summary, the shaft of stainless steel or other metal alloy in rubber rollers provides additional strength and protection, ensuring the roller’s longevity and performance in various industrial applications.
Layer of Elastomer Material
The layer of elastomer material used in rubber rollers plays a crucial role in enhancing their performance and durability. Elastomer material is added to the rubber compound during the rubber compounding process to modify the final properties of the roller. This layer of elastomer material helps improve the roller’s weathering resistance, chemical resistance, and overall resilience.
Various compounding ingredients are added to the elastomer material during the rubber compounding process. Fillers systems reinforce the rubber matrix and improve its mechanical properties. Common fillers used include carbon black, silica, and clay. Plasticizers are also added to increase the flexibility and elongation of the rubber compound. Stabilizer systems are incorporated to enhance the resistance of the roller to ageing, oxidation, and UV radiation. These systems typically consist of antioxidants and UV stabilizers. Lastly, vulcanizing agents are included to cross-link the rubber molecules and give the roller its final shape and strength.
In specific applications such as flexographic printing, elastomeric ink fountain rollers are made with this layer of elastomer material. These rollers possess excellent ink transfer properties, crucial for achieving high-quality print results.
Overall, the layer of elastomer material used in rubber rollers and the compounding ingredients ensures desirable properties such as chemical and weathering resistance, making them suitable for a wide range of industrial applications.
Frequently Asked Questions
What materials are typically used in the construction of precision rollers?
Typically, precision rollers are constructed using materials like high-grade steel, aluminum, silicone, polyurethane, fluropolymers(ie Teflon), foam and rubber. Sometimes, ceramic or plastic may be used depending on the specific requirements of the application they’re used in.
Can precision rollers be customized to suit specific industrial applications?
Yes, customization is a common practice in manufacturing equipment for specific industrial needs. This includes the ability to modify factors such as size, material, and other specifications to meet unique application requirements.
Are there any safety concerns or precautions to consider when using precision rollers?
Yes, safety concerns exist when using precision rollers. Precautions include ensuring proper training for operators, regular maintenance of the equipment, and use of appropriate safety gear to prevent injuries from potential accidents.
What are some common issues or malfunctions that can occur with precision rollers and how can they be troubleshooted?
Common issues with precision rollers include bearing failure, misalignment, contamination, material fatigue and surface wear. Troubleshooting can involve regular maintenance, alignment checks, and replacement of worn out parts to ensure smooth operation.
What is the typical lifespan of a precision roller and does it vary depending on the frequency of use?
The lifespan of a precision roller varies greatly, often depending on usage frequency. With regular use, they can last several years but may need replacement sooner with heavy or continuous use.
How do precision rollers contribute to the welding process in inertia friction welding, particularly in terms of accuracy and efficiency?
Precision rollers play a key role in inertia friction welding by ensuring accurate and efficient alignment and rotation of the parts being welded. Their precision is vital for maintaining the correct pressure and speed during the welding process, leading to strong, high-quality welds.
- Acoustic barriers for heat pumps
- Laminated Products
- Slitting & cutting
- 2D contour cutting
- Flat bed & rotary die cutting
- Laminating
- Drilling
- UR-foams 12-650 kg/m3
- Polyethylene, melamine resin, composite, synthetic EPDM and filter (15-80 ppi) foams
- Heavy layer (bitumen)
- Fleece (non-wovens)
- Self-adhesives
- Foils (PET, copper, fleece, aluminum)
- Low fogging / low emission
- FMVSS 302, UL94, DIN4102
- Temperature range -40°C – 180°C
- Oleo phobic and hydrophobic
- Acoustic test (alpha cabin, acoustic impedance)
- Customized product development and engineering support with 50+ years of experience.
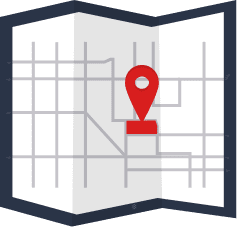
Find your local Enbi facility to enquire about our Precision Rollers.

Urgent technical question? Contact our experienced engineers for advice.