Enbi Group is a leading provider of lamination rollers, trusted by top OEMs and suppliers worldwide. We specialize in the design, manufacturing, and processing of premium lamination rollers, delivering reliable solutions for diverse industrial applications.
With a strong global presence and a North American base, we ensure seamless delivery to key markets across all major continents. Our commitment to innovation drives us to invest in advanced equipment and cutting-edge methodologies, ensuring exceptional quality, precision, and efficiency in every product we deliver.
Choose Enbi Group for durable, high-performance lamination rollers designed to meet the demands of modern industries.
Lamination Rollers: Essential Components for Quality Laminating
A lamination roller is a vital component of laminator machines, widely used across industries to apply a protective plastic film to various materials such as documents, photographs, and labels. These rollers are typically made from durable materials like silicone rubber and are designed to ensure even pressure and smooth movement during the lamination process.
By providing consistent, bubble-free results, lamination rollers enhance the durability, appearance, and protection of laminated items. Depending on the machine and materials, rollers may operate as heated or cold components, facilitating the adhesion of the plastic film to the substrate.
Why Lamination Rollers Are Important
Lamination rollers play a crucial role in producing high-quality laminated products. They ensure the plastic film adheres securely to the material, delivering a professional finish that withstands wear and tear. Whether used in commercial or personal applications, these rollers are key to achieving reliable and long-lasting results.
Benefits of Using Lamination Rollers
Lamination rollers are vital for ensuring smooth, high-quality results in the laminating process. By applying even pressure, they create a flawless, wrinkle-free finish that protects documents, photos, and other materials from damage. These rollers enhance productivity and simplify lamination, making them indispensable for businesses and professional use.
Built for Durability and Strength
Crafted from durable rubber rollers, these components are designed to withstand constant use and high pressures. Their premium rubber or elastomer materials resist wear and high temperatures, ensuring long-lasting performance. Features like ball-bearing mechanisms deliver smooth, consistent operation, making them a reliable choice for demanding lamination tasks.
Versatile for a Range of Applications
Lamination rollers excel in handling diverse materials, from documents and ID cards to adhesive coatings. Whether using heat or pressure, they ensure uniform application for a professional finish. Their flexibility makes them ideal for various industries, meeting the needs of different laminating processes with precision and reliability.
A Cost-Effective Lamination Solution
Investing in lamination rollers reduces reliance on outsourcing services, saving time and money. Their durability and extended lifespan mean fewer replacements, while in-house lamination eliminates service fees and delays. Lamination rollers are a smart, cost-effective choice for businesses seeking efficient, high-quality results.
Different Types of Lamination Rollers
Lamination rollers are essential for achieving smooth, high-quality results in various lamination applications. Whether for hot lamination or cold lamination, these rollers play a vital role in ensuring durability, precision, and efficiency in the process.
- Hot Lamination Rollers: Designed to evenly distribute heat, these rollers ensure a strong bond between plastic film and materials, resulting in smooth, bubble-free finishes. Made from durable materials like silicone rubber, they are ideal for high-volume projects requiring speed and consistency.
- Cold Lamination Rollers: Perfect for pressure-sensitive adhesive films, these rollers operate without heat, offering a cost-effective solution for laminating delicate items like documents and photographs. Typically crafted from synthetic rubber, they provide reliable adhesion and protection.
- Resin Application Rollers: Specialised for even resin distribution, these rollers are used in laminating paper, fabric, and other materials. Their precision design prevents excess resin buildup, ensuring a professional finish.
Advantages of Lamination Rollers
- Durability and Strength: Lamination rollers, especially those made from durable rubber rollers, are built to withstand repetitive use, high pressures, and various temperatures, ensuring long-lasting performance.
- Versatility: From laminating documents and photos to adhesive coatings, lamination rollers handle diverse materials and applications, catering to different industry needs.
- Cost-Effectiveness: Investing in quality rollers reduces outsourcing costs and improves in-house lamination efficiency, making them an economical choice for businesses.
Sets of Laminating Rollers
Lamination machines often use roller sets to ensure consistent pressure and optimal results. These sets, including guide rollers, pull rollers, and pressure rollers, are designed for specific steps in the lamination process. Materials such as high-release silicone compounds for hot rollers and synthetic rubber for cold rollers ensure flawless finishes across applications.
Why Choose Quality Lamination Rollers?
High-quality lamination rollers are essential for professional results, offering durability, precision, and reliability. Whether for heat-based or pressure-sensitive applications, selecting the right rollers enhances productivity and ensures long-lasting laminated products.
Laminating Roller Materials
The choice of roller material is crucial to achieving reliable and durable lamination results. Different compounds are suited for specific lamination processes, ensuring proper adhesion and longevity.
- High-Release Silicone Compounds: Ideal for hot lamination, these materials resist high temperatures and create strong, long-lasting bonds between plastic film and documents. Silicone rollers ensure smooth operation and are perfect for heat-based lamination projects.
- Synthetic Rubber Compounds: Recommended for cold lamination, synthetic rubber offers excellent adhesion at low temperatures. These rollers are suitable for heat-sensitive materials, providing a reliable bond without the need for heat.
- Polyurethane Compounds: Versatile and durable, polyurethane works well in both hot and cold lamination. It offers consistent adhesion across various applications, making it a flexible choice for diverse laminating needs.
Key Considerations for Roller Material Selection
- Temperature Tolerance: Choose materials that align with the lamination machine’s operating temperatures to prevent poor adhesion or roller damage.
- Load and Pressure: Ensure the material can withstand the pressure applied during lamination for optimal bonding and performance.
- Application Needs: Select the material based on the type of lamination (hot or cold) and the sensitivity of the items being laminated.
Investing in the right laminating roller materials ensures high-quality results and extends the life of your rollers, making them a valuable component of any lamination process.
Get a Quotation
Let us know how about your lamination roller requirements.
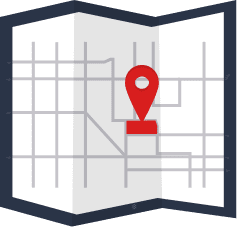
Find your local Enbi facility to enquire about our Lamination Rollers

Please contact our experienced team of engineers for any advice about lamination rollers.