Enbi Group is a global leader in industrial rubber rollers, partnering with top OEMs and tier-one suppliers to deliver precision-engineered solutions. Our expertise spans advanced technologies like Inertia Welding, rubber roller manufacturing, and roll forming techniques, ensuring unmatched quality and performance.
With a dependable supply chain supported by our North American hub and operations across four continents, we meet the demands of industries worldwide. We continually invest in cutting-edge tools and equipment to innovate and enhance the durability, efficiency, and cost-effectiveness of our rubber roller solutions.
Did you know that Inertia Welding can reduce waste by up to 30% and lower the weight and cost of an industrial rubber roller by as much as 25%? Trust Enbi for superior industrial rubber roller manufacturing that drives performance and value for your business.
A rubber roller is a cylindrical device made of rubber used in various industries for different applications. It is known for its wide range of uses and desirable properties, such as excellent resistance to wear and tear, heat resistance, and dimensional stability. The outer layer of the rubber roller is typically made of elastomer compounds, which provide a smooth and durable surface.
The paper industry uses rubber rollers for paper transport and laminating processes. It is also used in various other industrial applications, as well as in ATM and ticketing applications. The manufacturing process of a rubber roller involves covering a core, typically made of stainless steel or other rigid material composites, with a layer of elastomer material. This pattern on the surface of the roller is key for its functionality and individually engineered. With its versatility and durability, the rubber roller has become an essential tool in many industrial and manufacturing processes.
Rubber rollers are widely used in various industries due to their excellent resistance to wear and tear, desirable properties, and wide range of applications. Different types of rubber rollers are specifically designed to meet various industrial needs.
One type is the rubber drive roller, used for movement and conveying materials in industrial settings. These rollers are commonly found in manufacturing processes, particularly in the paper industry, where they play an integral role. Rubber drive rollers provide dimensional stability and a smooth surface for the efficient movement of materials.
Another type is the rubber conveyor roller, used as a moving system component. Made from durable rubber with a robust core, these rollers are commonly used in industrial applications for transporting heavy loads. They are known for their strength, durability, and long service life.
Grooved rollers are another type of rubber roller that is used in various industries. They have a specific grooved pattern on the surface, which allows for better grip and control during the conveying process. Grooved rollers are commonly used in applications requiring precise movement and control.
Silicone rubber rollers are also highly sought after for their heat resistance. They are commonly used in laminating processes, where high temperatures are involved. Silicone rubber rollers are known for their excellent thermal properties, making them suitable for applications in which heat resistance is crucial.
In conclusion, several types of rubber rollers are available for various industrial applications. Rubber drive rollers, rubber conveyor rollers, grooved rollers, and silicone rubber rollers have specific uses and advantages. Their durability, heat resistance, and precision make them indispensable components in many manufacturing processes.
Characteristics of Rubber Rollers
Rubber rollers are versatile components used in various industrial applications. They offer several desirable properties that make them indispensable in manufacturing processes. Firstly, rubber rollers provide excellent resistance to wear and damage, ensuring a long service life. They are also known for their heat resistance, allowing them to withstand high temperatures in applications like laminating. The outer layer of rubber rollers is typically made of elastomer compounds, providing a smooth and durable surface for efficient material movement. Additionally, rubber rollers come in different types to cater to specific needs, such as grooved rollers for precise control and silicone rubber rollers for applications requiring heat resistance. Overall, the wide range of rubber roller options and their exceptional physical characteristics make them crucial in various industries, from printing to manufacturing.
Durability and Strength
Rubber rollers are known for their exceptional durability and strength. They are designed to withstand high impact and vibrations, making them ideal for heavy machinery and equipment applications. The rubber’s ability to absorb shocks and vibrations ensures smooth operation and extends the lifespan of the roller.
One of the key advantages of rubber rollers is their non-marking property. They do not leave marks or scratches on the surfaces they come into contact with, which is crucial when working with delicate materials or finished products. This property also prevents damage to the roller itself, ensuring its longevity.
Another important aspect of rubber rollers is their customizability. They can be manufactured to meet specific requirements, allowing various applications across various industries. Rubber rollers can be tailored to provide the desired hardness, durometer, and surface finish, giving manufacturers the necessary flexibility.
Rubber rollers are particularly well-suited for applications that demand precision and material integrity. They are commonly used in printing, paper manufacturing, and laminating industries, where precise ink distribution and dimensional stability are critical. Additionally, rubber rollers are favored in industries where noise reduction and chemical resistance are important, such as the automotive, food, and pharmaceutical sectors.
In summary, the durability and strength of rubber rollers make them an excellent choice for a wide range of industrial applications. Their ability to absorb impact and vibrations, non-marring property, and customizability contribute to their long service life and effectiveness in various industries.
Heat Resistance
Rubber rollers’ heat resistance is a crucial characteristic that ensures their durability and reliability in various industrial applications. The ability of rubber rollers to withstand high temperatures is enhanced through a process called vulcanization. During vulcanization, rubber is mixed with specific chemical compounds, such as sulfur, and then subjected to heat. This process cross-links the rubber molecules, making them more heat, chemicals, and wear-resistant.
Different types of rubber materials are used to manufacture heat-resistant rubber rollers. Synthetic rubber materials like Styrene Butadiene Rubber (SBR), Ethylene Propylene Diene Monomer (EPDM), Silicone, Fluoroelastomers (FKM), and Chlorosulfonated Polyethylene (CSM) exhibit excellent heat resistance properties. SBR and EPDM are commonly used in lower-temperature applications, while Silicone, FKM, and CSM are favored for their exceptional resistance to high temperatures.
Heat resistance is particularly important in industries like paper, where rubber rollers are extensively utilized. In the paper manufacturing process, rubber rollers ensure smooth ink distribution and the proper alignment of paper sheets. These rollers are subjected to high temperatures due to the heat generated during high-speed printing. Using heat-resistant rubber materials, such as EPDM or Silicone, these rollers can withstand demanding conditions and maintain their performance over an extended service life. Overall, heat resistance in rubber rollers is vital for ensuring efficient operations and preventing premature failure in a wide range of industrial sectors.
Range of Sizes and Shapes
Rubber rollers come in various sizes and shapes to cater to various industrial applications. Customers can choose from different sizes and shapes depending on their specific requirements.
In terms of sizes, rubber rollers are available in many dimensions. They can range from small sizes, such as 30mm, to larger sizes, like 165mm or even bigger. This wide range ensures that customers can find the perfect size for their equipment or machinery.
Similarly, rubber rollers are available in various shapes to accommodate different needs. Common shapes include cylindrical rollers, grooved rollers, and laminating rollers. The cylindrical shape is versatile and ideal for applications requiring uniform ink distribution or dimensional stability. Grooved rollers, on the other hand, feature a grooved pattern on their surface, which is beneficial for specific printing or paper industry applications. As the name suggests, laminating rollers are used in laminating materials.
With a wide range of sizes and shapes, customers can choose the perfect rubber roller that suits their particular requirements. Whether it’s a small 30mm roller, a larger 165mm one, or a cylindrical, grooved, or laminating roller, there are plenty of options in the market.
Excellent Resistance to Abrasion and Corrosion
Rubber rollers are known for their excellent resistance to abrasion and corrosion, making them highly durable and reliable in various applications. Abrasion resistance refers to the roller’s ability to withstand wear and tear caused by friction and contact with other surfaces. Rubber rollers, with their strong and resilient nature, can withstand repeated use without experiencing significant damage or loss of performance.
Moreover, rubber rollers exhibit remarkable corrosion resistance, the gradual deterioration caused by chemical reactions or exposure to corrosive substances. This resistance allows rubber rollers to maintain structural integrity and functionality even in harsh environments or corrosive substances commonly found in industrial settings.
This exceptional resistance to abrasion and corrosion makes rubber rollers highly beneficial in various applications. Industries such as printing, packaging, paper, textile, and converting rely on rubber rollers to withstand continuous contact with various materials, chemicals, and processes. Rubber rollers are also commonly used in manufacturing processes such as laminating, embossing, and coating, where they need to withstand prolonged exposure to chemicals, heat, and mechanical stress.
In summary, the excellent resistance of rubber rollers to both abrasion and corrosion makes them an ideal choice for industries and processes where durability and longevity are essential. Their ability to withstand wear and tear, along with corrosive substances, ensures a longer service life, reduced maintenance costs, and optimal application performance.
Desirable Properties for Specific Applications
Rubber rollers possess several desirable properties that make them ideal for specific applications. One key property is their durability, which allows them to withstand continuous contact with various materials, chemicals, and manufacturing processes. This durability ensures a longer service life, reducing maintenance costs and increasing operational efficiency.
Another important property is the traction provided by the rubber surface of the roller. This traction allows for effective gripping and ink distribution in the printing and packaging industries, ensuring uniform and high-quality results in applications such as laminating or embossing, the traction of rubber rollers aids in achieving precise and consistent patterns or textures on materials.
The versatility of rubber rollers is also a significant advantage. They can be customized with specific rubber types and surface patterns, allowing them to be used in diverse applications such as the paper industry, textile manufacturing, and marine applications. This versatility ensures that rubber rollers meet various industries’ specific requirements and demands, improving overall efficiency and product quality.
Overall, the desirable properties of rubber rollers, including durability, traction, and versatility, play a vital role in improving efficiency and enhancing quality in industries such as printing, packaging, paper, textile, and converting. These properties enable rubber rollers to withstand harsh environments, maintain optimal performance, and deliver consistent results, making them indispensable in numerous specific applications.
Materials Used in the Manufacture of Rubber Rollers
The materials used in rubber rollers are crucial in determining their performance and suitability for various applications. Rubber rollers are typically made using elastomer compounds, which provide the desired properties such as excellent resistance to wear, heat, and chemicals. These elastomer compounds are applied as a layer on roller cores, often made of materials like stainless steel or rigid composites. The outer layer of elastomer material provides the necessary traction and grip for effective ink distribution in the printing and packaging industries and ensures dimensional stability and durability. Depending on the specific application, different types of rubber can be used to achieve the desired performance characteristics, such as natural rubber, silicone rubber, or synthetic rubber. The use of high-quality materials and advanced manufacturing processes contributes to rubber rollers’ long service life and reliability, making them an integral component in various industrial and commercial sectors.
Natural Rubber
Natural rubber is a versatile and widely used material in various industries, particularly in manufacturing rubber rollers. With its unique characteristics and properties, natural rubber offers excellent heat buildup and fatigue resistance, making it highly desirable for such applications.
One of the key advantages of natural rubber is its exceptional heat resistance. It can withstand high temperatures without deforming or losing its integrity. This makes it ideal for use in industries where heat buildup is common, such as the paper industry. Natural rubber exhibits excellent fatigue resistance, which can withstand repeated stress and strain without experiencing significant wear or damage.
Furthermore, natural rubber’s desirable properties contribute to its effectiveness as a roller cover material. It offers superior dimensional stability, ensuring the roller maintains its shape and performs optimally over its service life. The grooved pattern on the surface of the roller helps with ink distribution and provides better traction. Moreover, natural rubber’s physical characteristics, such as its elasticity and flexibility, allow it to conform to various roller cores and integral shafts.
In summary, natural rubber is an excellent choice for manufacturing rubber rollers due to its heat buildup and fatigue resistance. Its desirable properties, including dimensional stability and ink distribution capabilities, further enhance its functionality in industrial applications.
Layer of Elastomer Compounds (Elastomers)
In the manufacturing process of rubber rollers, a layer of elastomer compounds, known as elastomers, is used to provide the necessary properties and performance characteristics. Ethylene propylene rubber (EPM/EPDM) is a commonly used elastomer compound.
Elastomers like EPM/EPDM are polymerized during manufacturing to achieve desirable characteristics. One of the key benefits is their excellent weathering resistance, which allows the rubber rollers to withstand exposure to outdoor elements without degrading or losing their performance. This makes them suitable for a wide range of industrial applications.
Also, elastomers like EPM/EPDM exhibit superior insulating properties, making them ideal for electrical and electronic industries. They can effectively resist the flow of electric current and provide a protective barrier against electrical hazards.
Moreover, elastomers offer excellent mechanical properties at both high and low temperatures. They can withstand extreme temperature variations without losing their elasticity or flexibility, ensuring optimal performance of the rubber rollers in various environments.
Elastomers can be cured using sulfur or peroxide, enabling the rubber rollers to maintain their shape and integrity during use. This curing process enhances their durability and resistance to physical stress.
Furthermore, elastomers possess good chemical resistance, allowing them to withstand exposure to various chemicals and substances without damage or degradation. This makes them suitable for use in industries where contact with chemicals is common.
In conclusion, the layer of elastomer compounds, such as EPM/EPDM, used in manufacturing rubber rollers provides excellent weathering resistance, insulating properties, and mechanical strength at high and low temperatures. Their ability to be cured and their chemical resistance further enhance the durability and performance of rubber rollers.
Shaft of Stainless Steel or Other Metal Alloy
The core of shaft of rubber rollers is often made of stainless steel or other metal alloys, providing additional strength and protection to the roller. This outer layer acts as a core, offering resistance against external forces and is key for the durability of the roller.
Using stainless steel or other metal alloys in the shaft enhances the durability and longevity of the rubber roller. These materials have excellent tensile strength, allowing the roller to withstand heavy loads and pressures without deformation or failure. They also offer corrosion resistance, ensuring the roller performs even in harsh environments.
Different types of metal alloys are commonly used to manufacture rubber rollers. Stainless steel is a popular choice due to its high durability, corrosion resistance, and ability to maintain its physical properties at various temperatures. Other metal alloys, such as aluminum or rigid material composites, may also be used depending on the specific application requirements.
In summary, the shaft of stainless steel or other metal alloy in rubber rollers provides additional strength and protection, ensuring the roller’s longevity and performance in various industrial applications.
Layer of Elastomer Material
The layer of elastomer material used in rubber rollers plays a crucial role in enhancing their performance and durability. Elastomer material is added to the rubber compound during the rubber compounding process to modify the final properties of the roller. This layer of elastomer material helps improve the roller’s weathering resistance, chemical resistance, and overall resilience.
Various compounding ingredients are added to the elastomer material during the rubber compounding process. Fillers systems reinforce the rubber matrix and improve its mechanical properties. Common fillers used include carbon black, silica, and clay. Plasticizers are also added to increase the flexibility and elongation of the rubber compound. Stabilizer systems are incorporated to enhance the resistance of the roller to ageing, oxidation, and UV radiation. These systems typically consist of antioxidants and UV stabilizers. Lastly, vulcanizing agents are included to cross-link the rubber molecules and give the roller its final shape and strength.
In specific applications such as flexographic printing, elastomeric ink fountain rollers are made with this layer of elastomer material. These rollers possess excellent ink transfer properties, crucial for achieving high-quality print results.
Overall, the layer of elastomer material used in rubber rollers and the compounding ingredients ensures desirable properties such as chemical and weathering resistance, making them suitable for a wide range of industrial applications.
Uses and Applications of Rubber Rollers
Rubber rollers have a wide range of uses and applications across various industries. Rubber rollers are commonly used for ink distribution in the paper industry, providing precise and consistent ink coverage during printing processes. They are also used in laminating rollers for applying adhesive and ensuring proper bonding of materials. Rubber rollers are crucial in manufacturing various products, including tapes, labels, and packaging materials, where they help maintain dimensional stability and ensure uniformity. In industrial applications, rubber rollers convey materials, guide and support equipment, and provide traction in various machinery and systems. Rubber rollers are also frequently employed in ATM and ticketing applications. Overall, rubber rollers play a vital role in numerous industries by providing desirable properties such as heat resistance, excellent resistance to damage, and precise ink transfer capabilities.
Paper Industry
Rubber rollers play a vital role in the paper industry, particularly in the printing and converting processes. Rubber rollers are essential for achieving high-quality prints, Whether flexographic, gravure or offset printing. Additionally, they are used in paper, film, and foil converters for various applications.
One of the key functions of rubber rollers in the paper industry is ink distribution. The even distribution of ink is crucial for producing clear and vibrant prints. Rubber rollers ensure that ink is spread evenly across the printing surface, resulting in consistent and smooth printing.
Moreover, rubber rollers offer dimensional stability, vital for precise printing. They help maintain accurate measurements and enable high-quality fine details to be reproduced. This ensures that prints look crisp and clear, enhancing the overall quality.
Rubber rollers also provide a grooved pattern on the printing surface, improving the grip between the roller and the substrate. This enhances the printing quality by preventing slippage during the process, resulting in better registration and sharper image reproduction.
In addition to their functional benefits, rubber rollers are known for their durability, resistance to abrasion and corrosion, and excellent heat resistance. These properties make them suitable for the demanding environment of the paper industry, where they are exposed to constant friction, chemicals, and elevated temperatures.
Rubber rollers are indispensable in the paper industry for achieving excellent ink distribution, dimensional stability, and grooved pattern. Their durability and resistance to various types of damage contribute to their long service life, making them an essential component in the printing and converting processes.
Other Types of Rollers
Within this article, many features of rubber rollers have been mentioned. There are also other important types of rollers, such as those that have polyurethane (PU/PUR) as a coating. Here it is possible to mold the polyurethane directly around the shaft or to apply a polyurethane foam to the shaft and subsequently grind it to the required geometry.
Get a Quotation
Please complete the form below telling us about your industrial rubber roller requirements.
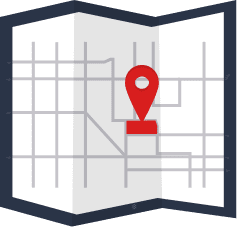
Find your local Enbi facility to enquire about our industrial rubber rollers.

Urgent technical question? Contact our experienced engineers for advice.